Heat Transfer Fluid Systems Provide Consistent Heat—Keeping Asphalt Cement Moving to Where It Is Needed
HEAT TRANSFER FLUIDS VS. LOW-COST BASE OILS
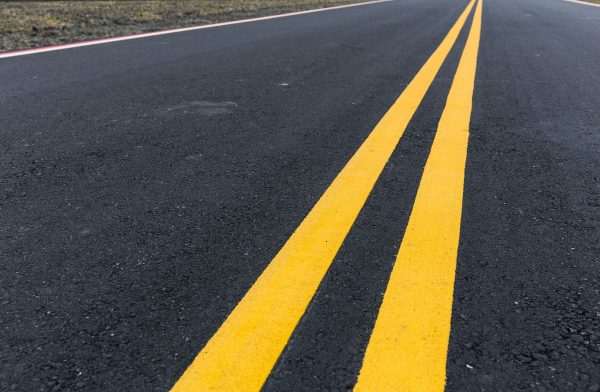
Heat Transfer Fluids (HTF) are designed and rated to maintain consistent temperatures for asphalt plants.
Problems occur when there is a sudden loss of fluid from the system causing it to shut down. Because delivery schedules need to be kept, some asphalt contractors will “top off” a system with any oil that happens to be on hand just to keep the operation moving.
The damage that can be done to a system in the long term makes using low-cost oils a bad decision.
Motor oil, turbine oil, hydraulic oil, R & O (Rust and Oxidation) lubricants, and common base oils are simply not designed to perform under the continuous high operating temperatures of a heat transfer fluid system.
These oils along with “multi-purpose oils” sold by some companies as HTFs can be unreliable because the additives in them are designed for the needs of other applications.
Once these additives are used up all that is left is poorly refined base oil. Sludge build-up can reduce heat transfer rates and in serious cases can plug a system completely. This will cause a plant to shut down, and require cleaning the entire system.
ROUTINE MAINTENANCE KEEPS ASPHALT PLANTS RUNNING SMOOTHLY
In asphalt plants with thermal oil heaters, safety and performance are greatly improved through proper maintenance. A program of routine checks keeps systems running at their best.
- Conduct an annual fluid analysis. Use a clear glass container and take the sample from a “live” part of the system such as a blow down valve on the Y-strainer or a low drain point. Allow a couple quarts to flow into a separate container; this will assure a representative sample. Then take the sample when the fluid is between 180° and 230°F. Examine the oil, look for particles suspended in the oil. Second, check the viscosity. Higher viscosities are produced when oil is oxidized or contaminated. Third, send the sample into Paratherm for a Fluid Analysis.
- Keeping the Y strainer clean will prolong the life of your fluid charge, and help the system run smoothly.
- Use proper start-up and shut down procedures. To save on fuel costs, some plant owners shut down heaters at night, on weekends and during cold seasons. When starting up, bring the heater outlet gradually up to 200°F and then continue, up to operating temperature. This will avoid overheating the fluid. When shutting down leave the combustion air blower and the circulating pump running until the fluid temperature is down to 200F
- Check insulation to see if it is wet with fluid. Soaked insulation can spontaneously ignite. Using closed cell insulation or removing insulation altogether from potential leak points is recommended. Smoke is a sure sign that fluid is leaking.
- Check the low level switch to make sure it is functioning. Sludge can build up in the expansion tank causing the float switch to hang up. This can allow the system to continue to operate with a dry tank causing severe degradation of the fluid.
- Remove water by draining a small amount of fluid from the bottom of the expansion tank.
- Drain the catch container or Buffer tank. Never put oil found in the catch container back in the system.
- Check the stack temperature versus the heater outlet temperature. If the stack temperature is higher than normal, you either have soot buildup on the outside of the coils or coke buildup inside the coils.
HOT OIL SYSTEMS FOR ASPHALT PLANTS
Thermal Fluid Systems are used to heat the asphalt tanks, mix plants and storage silos that supply paving material to one of the largest cities in the west coast. The city has over 6,000 miles of streets and repaves about 270 miles in a typical year, not including repairing potholes and emergencies. Two plants supply the city’s needs. One of the two plants is a 5,000 pound batch plant that prepares, 300,000 tons of asphalt a year, or 1,600 tons of asphalt every working day. The asphalt is pumped into liquid storage tanks, and sent through a piping system to the weigh scales. Here it is mixed with 3/8”, 1/2” and 3/4” aggregate which had been previously heated to 340°F to remove any residual water. The mixed asphalt is then moved to storage silos, where it waits to be loaded into trucks for jobsite delivery. If there is bad weather like rain and crews cannot work, the heat transfer fluid has to keep the asphalt hot at the plant for up to a week or more.
It is imperative that the plant runs smoothly just to keep up because any delays that slow or temporarily halt production can put the city seriously behind schedule.
The city had been using various brands of heat transfer fluids, but over time they would begin degrading causing a loss of heating capability in the tanks. When enough heat was lost, jack hammers had to be used to remove hardened asphalt.
Paratherm NF solved this problem. When the fluid was analyzed it showed no signs of breaking down, as previous fluids had.
OTHER ARTICLES
Analyzing Your Fluid Paratherm User’s Guide
Thermal Fluid Safety Resources Paratherm WebPage